Safety is a top priority for the transport and logistics industry, especially when it comes to trailer fleets. Compared to their light commercial vehicle counterparts, heavy-duty trailer vehicles come with more weight, limited maneuverability and additional vehicle parts to consider (like the trailer itself).
While the goal is for smooth operation 24/7, trailers, like all vehicles, can experience dead batteries or flat tires. It’s been reported that the U.S. experiences 220 million flat tires each year. In those cases, calling for emergency roadside assistance is often the only repair option, but this route can be costly, put driver safety at risk and contribute to significant downtime.
While a time might come when you need to lean on these services, there are steps you can take to lessen the likelihood of calling for emergency roadside assistance – whether towing, tire changes, fuel delivery or battery boosting. The key is preventative trailer maintenance, and here are three ways MICHELIN Connected Fleet recommends to enhance your preventative maintenance strategy to avoid roadside assistance.
1. Use your vehicle data
The first step to kickstarting your preventative maintenance strategy is investing in telematics and fleet management systems that provide real-time data on the condition of your vehicle and trailer. It is imperative that vehicles and their equipment are operating in top condition to mitigate potential safety hazards. By setting up predictive maintenance alerts, you can monitor vehicle health and know when it is time for necessary repairs or maintenance check-ups.
These alerts also provide specific vehicle data, which can help inform business decisions and improve overall operational efficiency. By leveraging trailer data captured from door sensors, TPMS and GPS systems, fleet managers can better anticipate and control costs, including those related to detention and trailer maintenance. Take TPMS, for example; when you have the power to monitor tire pressures and temperatures, you can identify and correct trailer tire issues before they cause an emergency incident on the road.
2. establish regular inspections & preventative maintenance
Next, consider implementing regular vehicle inspections and a preventative maintenance schedule to stay one step ahead of possible breakdowns or safety concerns. Fleet managers can establish a comprehensive and regular trailer inspection schedule to check key components and equipment needs. Often, fleet managers work off of a maintenance checklist, listing out specific parts, including door sensors, TPMS sensors, GPS tracking and truck and trailer links. By analyzing each of these parts and more, you can identify any that are worn and in need of repair or replacement.
Routine inspections should be scheduled and performed regularly, whether weekly, monthly or annually, to ensure all trailer components operate efficiently and fall in line with maintenance checklist protocols. Pre-trip inspections are also encouraged to avoid accidents or roadside emergencies during longer route journeys. Preventative maintenance schedules are no longer a nice-to-have plan but should be an integral part of all trailer fleet management, alleviating downtime, maintaining equipment efficiency and preventing potential emergency roadside services.
3. prioritize driver training & communication
A final consideration for avoiding emergency roadside services is improving driver training and communication. Driver training sets the standard for all behavior that takes place on the road. By prioritizing training at the forefront, you can set your drivers up for success, improving safety, preventing costly delays and enhancing operations. It is recommended that drivers are trained to perform basic pre-trip and post-trip inspections, analyzing equipment performance and reporting any noticeable issues. This is a best practice for all drivers and helps with improving driver-to-management communication.
By establishing clear communication channels between drivers and maintenance teams, fleet managers can encourage a proactive reporting culture where drivers can feel more comfortable informing fleet management about any concerns or abnormalities with their vehicle. Stronger communication can also encourage safer driving behavior and training programs, empowering drivers to prioritize safety and responsibility on the road.
Trailer maintenance matters with MICHELIN Connected Fleet
Emergency roadside services are not to be taken for granted and are a valuable resource when needed. However, with the proper maintenance plan, fleet managers can avoid costly tire repairs, driver downtime, late deliveries and potential accident liability. By assessing your current needs and sourcing insights from predictive maintenance data and live trailer monitoring, you can continue to keep your drivers on the road, optimize your fleet’s trailer utilization and improve operational efficiency.
MICHELIN Connected Fleet offers best-in-class maintenance solutions geared toward your trailer vehicles and business. If you’re ready for a predictive maintenance plan tailored to your needs, contact us online or call 800-358-6178.
Reach Out to MICHELIN Connected Fleet to Learn More Today.
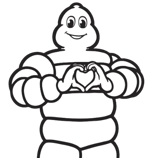
Written by The MICHELIN Connected Fleet Team
Other Interesting Stories
5 Tips for More Efficient EV Fleets
In this blog, we provide tips for fleet managers who have already switched to EVs, arming them with best practices to get the most out of their investment.
How Proper Trailer Maintenance Helps You Avoid Emergency Roadside Services
In this blog, we recommend three ways to enhance your preventative maintenance strategy to avoid trailer roadside assistance.
Truck & Trailer Pain Points: How to Boost Cost Control, Logistics & Productivity
In this blog, we pinpoint specific challenges for the transportation & logistics industry and share how fleet management solutions support ongoing goals.