Operating fleets of trucks and trailers comes with a set of unique challenges for fleet owners and managers. From rising costs and logistics hurdles to slowed productivity caused by downtime, businesses are tasked with streamlining operations in a highly competitive environment.
In this blog, the MICHELIN Connected Fleet team pinpoints a few specific pain points for the industry and shares how a first-class fleet management system can support your cost control, logistics and productivity goals.
The challenges
Like many others, the transportation and logistics industry is feeling the weight of increased costs, with the main driver being rising fuel prices. It is reported that fuel prices have grown to a $3.094 national average as of January 2024. These higher prices can create a domino effect within your fleet business, leading to higher operational and maintenance costs. When fuel costs are higher, fleet managers require more resources to monitor fuel spend and reallocate funds to keep up with the rising costs. Along with fuel prices, truck and trailer fleet managers constantly battle increased maintenance costs due to over-the-road wear and tear and unplanned maintenance repairs.
Another significant pain point is managing and tracking trucks and trailers once on the road. When it comes to logistics, the main priority is ensuring assets get from point A to point B. Issues can often arise during transportation when fleet managers are not equipped with the proper tracking or geolocation tools. Lastly, without proper preventative maintenance and safety protocols for your trucks and trailers, your business risks reduced productivity and loss of revenue.
the solutions
Armed with the right tools and tested strategies, truck and trailer managers can optimize their fleet’s performance with cost control, real-time tracking and preventative maintenance systems in place.
Monitoring Cost Control
While rising fuel prices can be unpredictable, truck and trailer fleet managers can monitor fuel spend and make necessary adjustments using fleet monitoring systems. With this technology, you are provided visibility into how much fuel is being used, where it is being used and how overall fuel impact can be reduced. These systems can also identify fuel system malfunctions and how inefficiencies impact repair and operational spending.
Similar to fuel’s impact on fleet maintenance, driver behavior has a significant effect on operational costs. When drivers exhibit riskier driving behavior like sharp turns and harsh braking, it can lead to unplanned maintenance repair and downtime. Additionally, when a specific trip consists of transporting heavy assets, drivers are at risk of operating overloaded trailers. To avoid paused operations, wasted resources and unsafe driving conditions, fleet managers can rely on data to review and address safety concerns before drivers hit the road.
Trailer managers can review and monitor cargo weight data and restrictions, analyzing how much each vehicle can handle per trip. Reducing truck and trailer spend has positive implications on fleet operations, leading to optimized fuel usage, less downtime and increased safety.
Managing Logistics
Real-time tracking is essential for any truck or trailer fleet management system to ensure assets reach their destination. For both asset and vehicle tracking, fleet managers can rely on geolocation tools and tracking technologies to know when specific trips are taking place and where vehicles are in their delivery journey. Monitoring systems can inform fleet managers of the exact location of their vehicles during a trip. This, in turn, opens the doors to route optimization opportunities, showcasing the fastest, most efficient routes, identifying potential nearby trips and prioritizing safety for drivers.
Geolocation tools also play a pivotal role when it comes to asset tracking. All assets are considered valuable, and to ensure they are protected and arrive on time, look to geofences. These virtual fence-like barriers establish a permitter around a fixed location so you can monitor where they are while setting up alerts to know if and when they leave the perimeter. Additionally, geofencing can also be a valuable resource in identifying excessive detention times. By knowing when a truck or trailer has entered a pre-defined area, fleet managers can more accurately track and account for detention from loading and unloading. With the right tools within your truck and trailer management system, you can seamlessly and efficiently keep tabs on your vehicles, drivers and assets.
Prioritizing Productivity
Maintaining productive fleet operations is no small task. From ensuring truck and trailer vehicles are in top-performing condition and compliant with industry standards to avoiding downtime and enhancing driver safety, there are many considerations that are top of mind when setting goals to operate more efficiently. A good place to start is working with a trusted industry partner who understands your business and can develop a scalable, unique plan tailored to your needs. Partners can analyze your budget, provide real-time tracking solutions and offer data analysis to produce positive results.
Truck and trailer fleets can achieve optimal productivity with the help of data and analytics. This data provides deeper insight into how your current operations are performing and where necessary changes can be made. For example, fleet managers can use GPS fleet management data to identify driving patterns, optimize routes and predict future maintenance needs. After analyzing your specific needs, industry partners can turn raw data into actionable insights and further develop solutions to solve ongoing challenges and enhance productivity.
rely on solutions from michelin connected fleet
As you review your current infrastructure and set goals at the start of the new year, consider putting your cost, logistics and productivity challenges in the hands of a trusted industry partner like MICHELIN Connected Fleet. Through our consultative approach, we can develop custom solutions for your fuel spending, driver safety and vehicle tracking needs, as well as provide the tools, technologies and data insights to move your business forward.
The MICHELIN Connected Fleet team is ready to solve your truck and trailer challenges and optimize your fleet operations. For more information, call 800-358-6187 or contact us online.
Reach Out to MICHELIN Connected Fleet to Learn More Today.
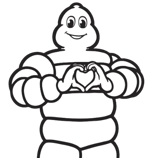
Written by The MICHELIN Connected Fleet Team
Other Interesting Stories
Maintenance
How Proper Trailer Maintenance Helps You Avoid Emergency Roadside Services
In this blog, we recommend three ways to enhance your preventative maintenance strategy to avoid trailer roadside assistance.
Cost Savings
Truck & Trailer Pain Points: How to Boost Cost Control, Logistics & Productivity
In this blog, we pinpoint specific challenges for the transportation & logistics industry and share how fleet management solutions support ongoing goals.
Productivity
Asset Tracking Fundamentals: Best Practices for 2024 Fleet Management
In our latest blog post, we highlight the asset tracking best practices to adopt in your 2024 fleet management strategy.