Managing a productive and efficient fleet is no small task. And when unexpected events like breakdowns or roadside incidents occur, it is critical to have an established maintenance plan in place to keep your trucks and trailers moving on the road. Implementing a preventative maintenance strategy is the best way to identify vehicle issues or equipment malfunctions before they escalate into potential safety hazards, and part of this strategy should include using automated Diagnostic Trouble Codes (DTC) alerts to stay one step ahead of the maintenance curve.
In this blog, MICHELIN Connected Fleet defines DTC alerts, outlines their value for preventative maintenance and lists ways to leverage these codes effectively for improved fleet safety and productivity.
WHAT ARE DIAGNOSTIC TROUBLE CODES?
DTC alerts are standardized codes used to identify and diagnose vehicle malfunctions. Generated by a vehicle’s onboard diagnostic (OBD) system, Diagnostic Trouble Codes send alerts about issues, including sensor malfunctions, fuel intake and emissions. With real-time data on vehicle performance and faults, DTC alerts support a proactive maintenance approach, guiding drivers and fleet managers to the specific component needing repair. By detecting issues early on, fleet managers can minimize downtime and avoid costly repairs while keeping vehicles in optimal condition.
THE VALUE OF DTC ALERTS IN PREVENTATIVE MAINTENANCE
A preventative maintenance strategy relies on real-time alerts and data for informed updates for swift and cost-efficient repairs. Fleet managers can see several benefits, including:
- Increased Vehicle Uptime
When trucks and trailers malfunction, repairs can take a long time, depending on the issue, causing operational downtime and slowed productivity. DTC alerts can help mitigate extensive downtime by identifying the source of the issue quickly, prompting fleet managers and technicians to work together on repairs or replacements.
- Early Problem Detection
DTC alerts provide fleet managers with a “heads-up” before truck and trailer issues take a turn for the worst. With real-time alerts, you can know the exact time a problem occurs and identify the root cause of the issue. Thanks to early problem detection, you can rely on DTC alerts to do the heavy lifting and kickstart the repair and maintenance process.
- Optimized Maintenance Schedules
All fleet managers know you cannot fully predict all truck and trailer incidents or breakdowns. So, it is essential to take a proactive approach with an organized, preventive maintenance strategy, anticipating repairs or replacements instead of reactively responding. By integrating Diagnostic Trouble Codes into your connected fleet maintenance plan, your team is armed with real-time alerts and data used to help your maintenance team make the necessary repairs.
- Cost Savings
Broken or damaged truck and trailer parts and components can quickly drive up costs, slow operations and affect your overall bottom line. Investing in a preventative maintenance strategy can help identify issues like increased fuel consumption and faulty parts that are costing your business. Through DTC alerts and real-time tracking, you can also evaluate if it is the right time to invest in higher-quality products or identify areas where you can reduce your fuel intake. This process helps extend the lifetime of your trucks and trailers and ultimately increase ROI.
LEVERAGING DATA WITH DTC ALERTS
Data is the cornerstone of any preventative maintenance strategy. Insights can be pulled from DTC alert data to help inform business decisions, such as investing in higher-quality equipment and reeducating drivers on safe driving behaviors. Training your drivers and staff on reading and interpreting DTC alert data is also important. Each code has a different meaning and pinpoints various areas within your truck or trailer. It is essential that you can identify the right malfunction or problem based on the specific code, so Diagnostic Trouble Code education is invaluable to your fleet management strategy.
IMPLEMENTING A PREVENTATIVE MAINTENANCE STRATEGY WITH MICHELIN CONNECTED FLEET
Truck and trailer breakdowns aren’t always avoidable. However, a preventative maintenance plan can lessen the burdens of costly downtime and delayed operations. DTC alerts can play a significant role in informing your strategy and overall business decisions with real-time alerts and data insights. MICHELIN Connected Fleet is here to help you make the most out of this data so your trucks and trailers can remain in top condition and support your business goals. Contact us today for more information.
Reach Out to MICHELIN Connected Fleet to Learn More Today.
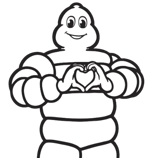
Written by The MICHELIN Connected Fleet Team
Other Interesting Stories
Operations
OEM Integration from MICHELIN Connected Fleet Simplifies Fleet Management
MICHELIN Connected Fleet's OEM integration streamlines light commercial vehicle management by providing direct access to data without extra hardware.
Maintenance
DTC Alerts & Truck and Trailer Preventative Maintenance Strategies
In this blog, MICHELIN Connected Fleet defines DTC alerts, outlines their value for preventative maintenance and lists ways to leverage these codes effectively for improved fleet safety and productivity.
Maintenance
Optimizing Fleet Performance with Better Brake, Light and Tire Maintenance
In this blog, MICHELIN Connected Fleet outlines how proper brake, light and tire maintenance can keep your fleets moving forward while supporting your bottom line and safety on the road.