Managing a fleet comes with its own set of challenges. From ensuring that vehicles operate efficiently to monitoring driver behavior, the job requires accurate, real-time data. Traditionally, fleet managers have been forced to use multiple disconnected systems to piece together this information, leading to delays and inaccuracies. With the latest OEM integration from MICHELIN Connected Fleet, fleet managers now have an easier way to access all the critical insights they need in one place.
A comprehensive fleet management solution helps fleet managers answer several essential questions that arise during normal operations. In this blog, MICHELIN Connected Fleet highlights the seven we frequently hear and how a connected fleet solution can solve your pain points and help you meet your unique business goals.
1. WHICH OF MY VEHICLES consume the most fuel?
Fuel is often one of the largest expenses for fleet operators, so managing fuel efficiency is crucial for reducing operating costs. An integrated fleet solution allows fleet managers to track fuel consumption across different vehicles, drivers and routes. By monitoring data such as idling time, route optimization and driver behavior, fleet managers can identify the vehicles or driving habits contributing to higher fuel use.
For example, harsh acceleration or frequent hard braking can lead to excessive fuel consumption. By addressing these issues through training or technology adjustments, fleet managers can help their teams adopt more fuel-efficient practices, ultimately reducing costs.
2. How can I access accurate odometer information?
Accurate odometer readings are essential for maintaining vehicles and ensuring compliance with regulations. However, manually tracking mileage can be time-consuming and prone to error. With a holistic fleet management solution, fleet managers can automatically access odometer information for every vehicle in their fleet. This eliminates the need for manual entry and ensures that data is always up-to-date. Current odometer data is especially useful for scheduling maintenance, tracking fuel tax requirements and ensuring vehicles stay compliant with regulations.
3. Are my drivers arriving on time?
Late arrivals can negatively impact customer satisfaction and lead to lost revenue opportunities. With an integrated fleet management solution, fleet managers gain access to live GPS tracking that provides precise, up-to-the-minute information on vehicle location and estimated time of arrival. Fleet managers can monitor route deviations and delays, adjusting routes as necessary to ensure drivers arrive on time. By keeping customers informed about ETA changes, fleet managers can enhance service reliability and customer trust.
4. do my drivers drive safely?
Driver safety is critical for reducing accident risk, lowering insurance costs and preventing vehicle damage. Comprehensive fleet management solutions allow managers to monitor driver behavior in real-time. By tracking metrics like speeding, hard braking, sudden acceleration and cornering, fleet managers can identify drivers who may be engaging in unsafe practices. Safety-related data can then be used for driver coaching, providing feedback and incentives to encourage better driving habits. With continuous monitoring, fleet managers can proactively address safety concerns before they escalate into accidents or unplanned maintenance events.
5. which of my vehicles require maintenance?
An integrated fleet management solution enables fleet managers to monitor vehicle health proactively. Using the most current data from the vehicle’s onboard diagnostics, fleet managers can receive automated alerts for issues like low tire pressure, oil changes, engine diagnostics and battery health. The system can predict when a vehicle will require maintenance based on odometer readings and diagnostic codes, helping managers stay ahead of breakdowns. By ensuring vehicles are serviced on time, fleet managers can extend vehicle life, improve operational efficiency and reduce the risk of costly repairs.
6. how can I reduce downtime and maintenance costs?
Unexpected downtime is one of the biggest challenges for fleet operators. An integrated fleet management solution helps reduce downtime by providing maintenance insights based on diagnostic data. For example, the system may detect a P0500 trouble code, indicating a malfunction in the vehicle speed sensor. This issue can affect critical safety systems like ABS and traction control, increasing the risk of incidents. By alerting fleeting managers to the problem early, the system enables proactive maintenance, reducing unplanned downtime and ensuring vehicles remain safe and operational while minimizing costly emergency repairs.
7. how do I get these business insights as quickly as possible?
With a fully connected solution, fleet managers can access all the data they need from one platform. For example, with MICHELIN Connected Fleet’s OEM integration, vehicle data is automatically gathered from the manufacturer’s systems, eliminating the need for manual data entry and reducing errors. This integration allows fleet managers to access critical insights instantly and make data-driven decisions quickly, whether it’s optimizing routes, managing fuel consumption or scheduling maintenance.
why choose an integrated fleet solution?
Fleet managers are under constant pressure to reduce fleet costs, improve safety and enhance operational efficiency. A comprehensive fleet solution allows them to do all this and more by providing holistic visibility into vehicle performance, driver behavior and maintenance needs. With MICHELIN Connected Fleet’s OEM integration, fleet managers gain access to accurate data that empowers them to make proactive decisions and drive better outcomes for their business.
If you're ready for better fleet insights with a single fleet management solution, contact MICHELIN Connected Fleet today.
Reach Out to MICHELIN Connected Fleet to Learn More Today.
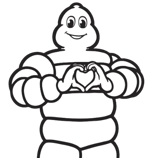
Written by The MICHELIN Connected Fleet Team
Other Interesting Stories
Operations
Go Beyond Fleet Tracking with MICHELIN Connected Fleet
In this blog, MICHELIN Connected Fleet outlines how its platform empowers fleet managers to make smarter decisions and stay ahead of the competition.
Operations
7 Questions Fleet Managers Can Answer with an Integrated Connected Fleet Solution
In this blog, MICHELIN Connected Fleet highlights the seven we frequently hear and how a connected fleet solution can solve your pain points and help you meet your unique business goals.
Safety
Spotlight on Camera Safety
MICHELIN Connected Fleet shares ways fleet managers can solve safety challenges with camera video monitoring solutions.