Vehicle downtime costs fleets hundreds of dollars per vehicle a day, and truck breakdowns that require assistance occur at a rate of every 10,000 miles. With tighter budgets than ever in a highly competitive transportation and logistics sector, keeping your trucks and trailers on the road is crucial. As they say in the industry: “if the wheels don’t turn, you don’t earn.”
In this blog, MICHELIN Connected Fleet highlights three key tips for keeping your fleet equipment out of the shop and on the road, cutting unexpected costs and ensuring on-time deliveries.
1. Keep a regular inspection & maintenance schedule
Adopting a regular inspection and maintenance schedule for your trucks and trailers, whether weekly, monthly or annually, is the best way to identify and address any problems.
Regular vehicle preventative maintenance includes oil changes, brake system inspections, tire checks and evaluation of any other systems vital to performance. This also extends to door sensors, TPMS sensors, GPS tracking and truck and trailer links. Standard maintenance costs are also well below the cost of emergency roadside assistance during a breakdown, an unexpected expense that is up 30% year over year on average.
Preventative maintenance also lowers drivers' safety risks. Without regular inspections, faulty vehicles may lead to brake system failures, steering system malfunctions or engine stalls. Proper vehicle maintenance also ensures drivers avoid delays or even fines from law enforcement personnel for operating faulty equipment.
2. use driver checklists
Incidents on the road not only put a driver’s and other motorists’ safety at risk, but result in vehicle downtime, lowering productivity and causing delays. Accidents on the road are a driving cause of downtime, leading to daily loss in revenue per vehicle. While proper training is crucial for preparing drivers, on-the-job safety practices can also go a long way to avoiding accidents and costly damage.
After your drivers complete their trips, they are required to complete their inspection checklists as part of their driver vehicle inspection report (DVIR). These post-trip reports can provide valuable data and insights about the health of your vehicle including fluid levels, steering and break mechanisms, fuel supply and more. Fleet managers can use this data to detect potential equipment malfunctions, improve operating conditions and ensure the safety of both drivers and vehicles.
3. make informed decisions with fleet management software data
There are many factors to consider when planning and executing successful fleet maintenance. Using your fleet management software is an efficient way to monitor vehicles, whether identifying system malfunctions, potential safety issues or gaps in driver training.
Consider working with a trusted industry partner who understands your maintenance needs and can help make the most sense of your fleet management software data. GPS fleet management software
provides data on driver behavior, equipment and fuel usage. A connected fleet partner can view this data and help identify harmful driving behaviors like idling that are wasting fuel, driving up costs and causing maintenance issues. Moreover, you have more visibility into equipment malfunctions that are slowing down operational efficiency or fuel inefficiencies that driving up costs. After you have analyzed all relevant data, you can better improve your drivers’ behaviors, vehicle health, route optimizations and operational spending.
Having the proper fleet management software is the first step in achieving your maintenance goals. However, working with a trusted partner in the field who understands your maintenance pain points turns data into insights can help you gain the most value out of your fleet management software.
prioritize your maintenance with MICHELIN Connected Fleet
The condition of your fleet directly impacts the safety of your drivers and your bottom line. Preventing accidents and expensive roadside assistance are the best ways to avoid vehicle downtime, keeping your trucks and trailers on the road.
Prioritize your fleet maintenance with MICHELIN Connected Fleet. We offer best-in-class maintenance solutions geared toward your trailer vehicles and business.
If you’re ready for a predictive maintenance plan tailored to your needs, call 800-358-6187 or contact us online.
Reach Out to MICHELIN Connected Fleet to Learn More Today.
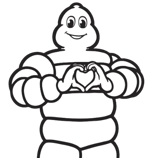
Written by The MICHELIN Connected Fleet Team
Other Interesting Stories
Operations
How to Improve Customer Experience by Improving Your Fleet Operations
In this blog, MICHELIN Connected Fleet highlights how improving fleet operations can directly translate into enhanced customer experiences.
Maintenance
Keeping Your Trucks & Trailers on the Road: 3 Maintenance Tips to Practice
In this blog, we highlight key tips for keeping your fleet out of the shop and on the road, cutting unexpected costs and ensuring on-time deliveries.
Safety
3 Ways to Focus on Fleet Safety During National Safety Month
MICHELIN Connected Fleet outlines three ways fleet managers can prioritize safety initiatives during National Safety Month.